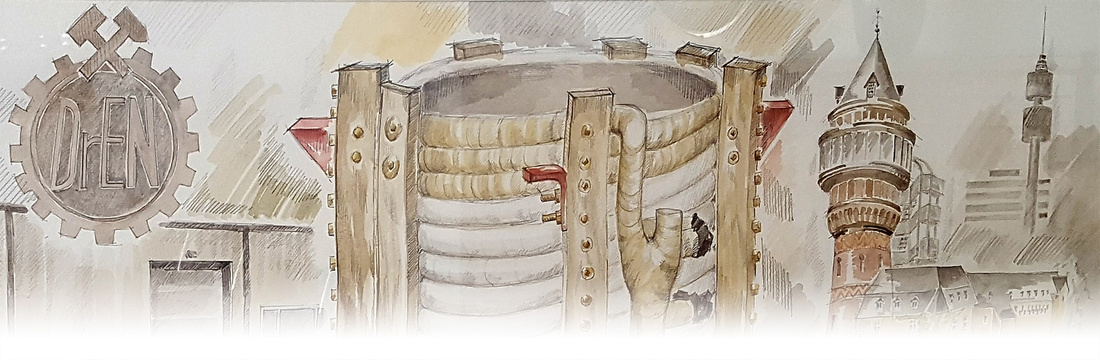
At the place where steel is heated, we feel at home.
Dr. Ewald Nelken GmbH
- founded in 1903
- 2500 m2 production area at 2 locations
- more than 40 employees
- no subcontractors and only experienced skilled workers and service technicians
- own flexible delivery service
- Development partner of plant and mechanical engineering and automotive / OEM
- Construction in two locations with SolidWorks
- certified since 1997 according to DIN ISO 9000
- 24-hour hotline at plant shutdown
Our story begins in 1903 - with a battery for mining. Ewald Nelken I. begins trading in NIFE steel batteries. It was followed by the first steel construction work and in 1920 the first series products for mining. The production grew and the children of the founder decided to divide the company into trade and production. This is how the companies Nelken & Co. Essen and Dr. Ing. Ewald Nelken oHG emerged. The structural changes in the mining and metallurgical sectors repeatedly changed the emphasis in production, from rail connectors to copper contact plates to cable suspensions and the construction of special metal construction solutions.
In 1962, the first inductor for the tempering of steel pipes was developed in cooperation with Mannesmann Roehrenwerke. The subject of inductive heating inspired us - and many customers with us. The tasks grew and the production area quickly became too small. So in 1968 we decided to build a bigger hall. Since no suitable building ground was found in Essen, we moved to the neighboring town of Muelheim in the new industrial park at the Rhine Ruhr harbor. The production halls in Muelheim were expanded in 1986 and 2008.
In 1992, the southern branch was founded in Heidenheim an der Brenz - between Aalen and Ulm in Baden Wuerttemberg. Numerous customers from the south of the country and the neighbors from Switzerland, Austria and France appreciated the short distance and fast reaction times. In 1999, we built our own production hall in Heidenheim, which was expanded in 2011.
Today we are a full service provider for inductive heating. With our partner, DM Montage- und Induktionsservice GmbH in Remscheid, we cover all requirements of preventive and acute maintenance. From the annual maintenance of the converter, to the short-term repair in case of failure, to the renewal of the cooling water hose and the general overhaul and new manufacture of inductors, material guide tubes and busbars.
In addition, we accompany you in challenging and consulting-intensive projects around inductive heating, from the idea to the commissioning of complex production lines.
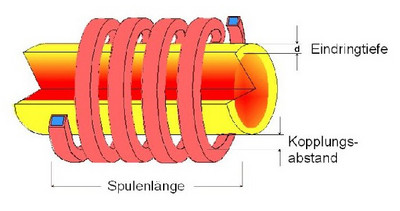
What are the inductors used for?
Many visitors to these sites are constantly dealing with inductive heating in their daily work lives. However, some business partners or interested parties know "induction" only from the basic knowledge of physics education. Therefore, the question of the location is not rare.
Induction technology is often used when machining metals of various shapes. The locations are very versatile and range from forming to tempering (hardening etc.).
If you imagine a classic forged part (eg a gearwheel), this is often transformed from a steel block. If the forging is hot worked (there is also cold forming), Induction heating is a relatively inexpensive process for heating the metals to forging temperature (about 1250 ° C). Another advantage is the ability to bring large quantities evenly and without high energy losses to forging temperature. The heated metal is then converted to the desired condition by means of presses or forge hammers.
Our job is to make and repair the tools that bring the heat into the metal. These tool families, also called inductors, are very versatile and adapted to the respective workpiece.
Simplified representation of inductive heating
Induction heating is a suitable technique for introducing energy into metallic parts. The well controllable heating, which takes place directly in the workpiece, is fast and can be limited to partial zones. Due to the reproducibility of the heating processes and the ease of handling, inductive heating is a technically mature process with a high degree of automation for industrial production. The most common applications are melting of steel and metallic alloys, heating of forgings for hot forming, annealing, normalizing and hardening, as well as bonding and sintering.
The induction systems are largely divided into three areas:
- Low Frequency Systems (up to 50 Hz)
- Medium frequency systems (up to approx. 10 kHz)
- High frequency systems (over 10 kHz)
The selection of suitable induction systems depends on the required degree of frequency-dependent current penetration depth in the workpiece:
- small workpiece diameter = higher frequency
- large workpiece diameter = lower frequency
Rule of thumb for an economical working frequency in steel heating: Material diameter = 2.5 - 7 x current penetration depth. At 3.5 times the penetration depth, the most favorable power transmission is achieved.
Mains frequency systems (50 Hz) can be connected directly to the three-phase network via adjustable transformers. Smaller facilities, for example, laboratory applications, soldering equipment, ball bearing heating, etc. can be operated in part with 230 V. mains voltage. Higher frequencies are generated in the frequency converters of the induction systems.
The tool of the induction system is the inductor, often called a coil. It consists of a single- or multi-turn water-cooled coil whose geometry is adapted as far as possible to the workpiece. The air gap (coupling distance) between the material to be heated and the coil influences the efficiency of the induction system.
According to the law of induction, a magnetic alternating field forms around a conductor through which an alternating current flows. In the metallic workpiece, which is exposed to the alternating magnetic field, eddy currents are induced, which heat the workpiece. The alternating magnetic field forces the eddy currents into the edge zone of the workpiece (skin effect) and causes heating of the edge zone according to the penetration depth. In the inlet region of the inductor, the temperature rise in the edge zone of the workpiece is very steep at the beginning. If the Curie temperature (768 ° C) is exceeded for ferritic steel, the permeability changes, the penetration depth increases and the temperature increase becomes somewhat flatter. The heating of the deeper zones in the workpiece to be heated is predominantly by heat conduction. The design of the inductor must be calculated so that the workpiece has the smallest possible temperature difference between the edge zone and the core when leaving the inductor.
The quality of a product is decisive for the image of a company. Our goal is to serve satisfied regular customers in the long term. To achieve this goal, quality plays a crucial role in our production processes. Before and during production, all articles are accompanied by work instructions and thoroughly checked before the goods are dispatched. With the delivery documents, our customers receive test instructions that document in detail the measured values of the incoming and outgoing inspections.
In order not only to sustain our quality of service in the long term, but also to permanently expand it, we have set up a process-structured quality management system according to the international standard DIN EN ISO 9001:2015 since 1997
In addition to our quality assurance guidelines, environmental protection plays an important role. The use of Euro and reusable packaging for plant transports is just as much a matter of course as the professional disposal of all non-organic products.
- Operation of the company location in accordance with all statutory and regulatory requirements and licensing permits
- Working according to all applicable environmental regulations
- Considering the latest technologies also from an environmental point of view in the procurement of new plants or modernization of existing plants while maintaining economic feasibility
- Consideration of neighborhood interests
- Reduction of environmentally detrimental factors
- Constant work in harmony with resource and energy saving production
- Use of water and energy-saving systems, for example of waterflow test bench in a rotating circuit.
- Download our terms and conditions or read online on the page AGB
- Heating curve for new bricked heating coils
- DIN EN ISO 9001:2015 Certificate of Dr. Ing. Ewald Nelken GmbH
- QM manual