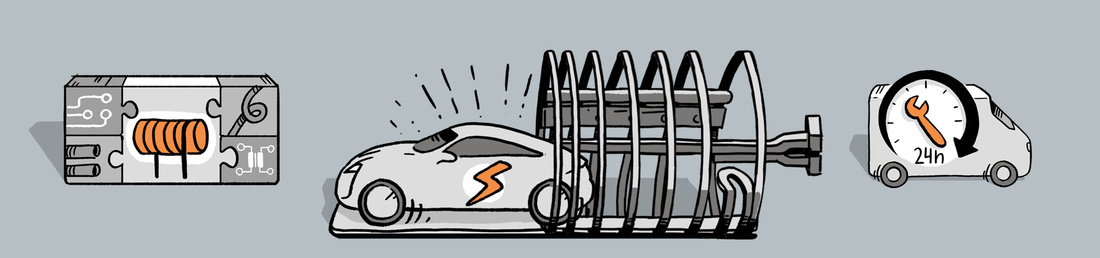
E-mobility and lightweight technology
The topic of "electromobility" that prevailed today at Dr. Ewald Nelken GmbH was already busy years before it spilled over to private car users. Over the past 10 years we have been able to deal with numerous applications that are essential for the development, research and production of electric vehicles. Current events and a rethink in society mean that alternative drives and energy-efficient solutions are becoming increasingly important and are developing from a niche product to a popular mass product. With this background, the necessary reductions in emissions in production, increasingly compact and complex technology and the desire for fully automated processes, the demands on technical solutions are also increasing at a rapid pace. With our inductive heating solutions, we are absolutely meeting the demand for decreasing cycle times, energy-optimized solutions, low emissions and high repeatability so as traceability of the results.
The Dr. Ewald Nelken GmbH is a full-service provider in the field of inductive heating and, with 60 years of its 117-year history, one of the most experienced companies in this segment. We develop appropriate processes and inductors, deliver all assemblies and create your turnkey inductive heating system.
In short, don´t hesitate to contact us for all matters relating to inductive heating.
In the field of e-mobility, we have been able to gain experience in almost every inductive application and bring a number of solutions to our customers.
Examples would be:
Stator production
- inductive shrink fitting (inductive joining) of stator and housing
- powder coating (hairpin stator)
- impregnation
Rotor production
- inductive joining of rotor shaft and rotor (heating from in- and outside)
- hard brazing/soldering of short circuit rings (asynchron motor)
- magnet bonding
Battery production
- heating of the housing to bring on plastic cooling bodies
- inductive drying
- inductive brazing/soldering of battery cable lugs
Others
- inductive (automated) brazing of capacitor pins and busbars
- inductive brazing of rails
- inductive hardening applications (gears, rotor shafts etc.)
- component contour heating
Lightweight construction in the automotive sector has also become significantly more important over the past two decades and is coming to the fore with new regulations and ever increasing targets with regard to pollutant emissions. The results are new material pairings, replacement solutions and alternative joining processes. Thanks to inductive heating and new manufacturing processes for inductors, solutions can now also be found that were not technically feasible a few years ago.
Examples would be:
- Alternative joining methods, for example with selective inductive heating of high-strength steel
- Inductive bonding of load-bearing parts
- Inductive partial surface heating of sheets made of high-performance materials
With over 60 years of experience in the field of inductive heating, we are pleased to be at your disposal as a full service partner for inductive heating systems.
Since we attach great importance to a system that is individually tailored to your needs, your wishes and requirements are in the foreground when designing your systems. We therefore always provide you with a coherent concept, from simple stationary heating to complex special solutions. The solutions developed in this way, consisting of converters, inductors, recooling, pyrometry, feeders, withdrawals, adjustments and also robotics, are available from us from a single source. Once your system is up and running, our comprehensive after-sale service will take care of you.
Please contact our sales department for advice on your individual projects.